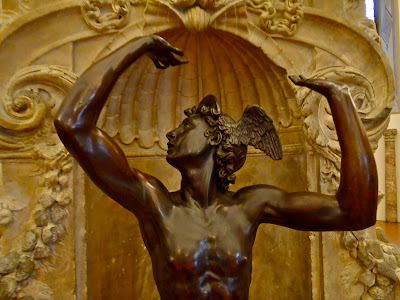 |
Mercury, Benvenuto Cellini, bronze 1550s, Bargello Museum, Florence |
During the renaissance, bronze sculptures cost a lot of money and few patrons could afford such expenditure in commissioning substantial bronze works for their private collections. Bronze cost about ten times as much as marble, and marble cost a lot. Bronze artefacts were associated particularly with antiquity. The Greeks had worked primarily in bronze, and elite renaissance society loved to emulate the ancients.
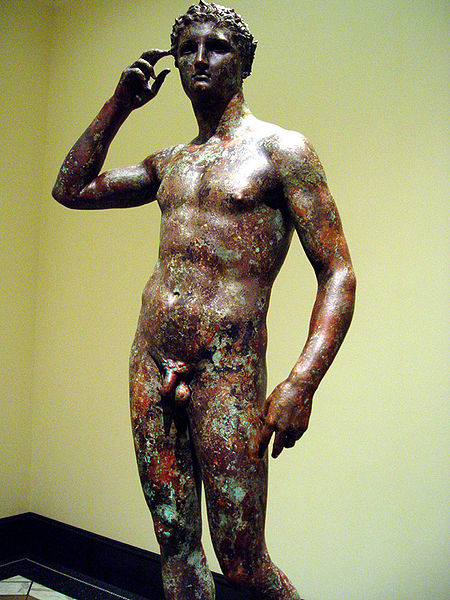 |
Athlete Crowning Himself, Greek, bronze, 300-100 BC, Getty Museum LA |
In the high renaissance, small statuettes would be very much in vogue as collectors’ items. The ancient Romans made marble copies of the superb bronze Greek original statuary and then melted down the bronze statues, using the metal for weapons and other more practical things. This helps explain why there are very few original Greek statues and so many copies of them. Due to the high tensile strength of bronze, statues of this material don’t need as much support base as the same statue in marble or stone. Knowing this, you can often guess when an ancient marble statue was a copy of a bronze. The marble statue will often have a tree trunk next to the leg of the figure which is purely structural; without it, it wouldn’t stand. What bronze statues did survive were often melted down during the medieval period to make church bells and canons.
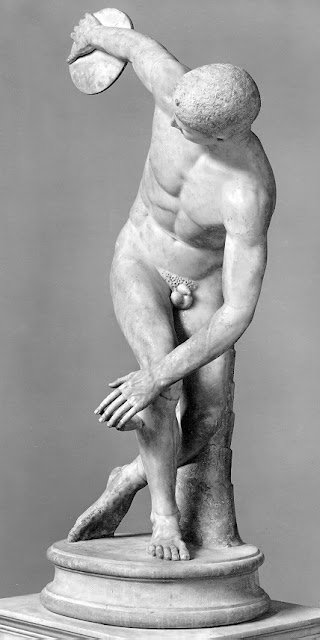 |
The Discus Thrower, Roman copy of Greek bronze, Hellenistic period |
Cosimo de Medici (known as Cosimo the Elder), in the first half of the 1400s, commissioned his favourite sculptor, Donatello, to cast a bronze David from the Old Testament. It was the first free standing nude bronze since antiquity.
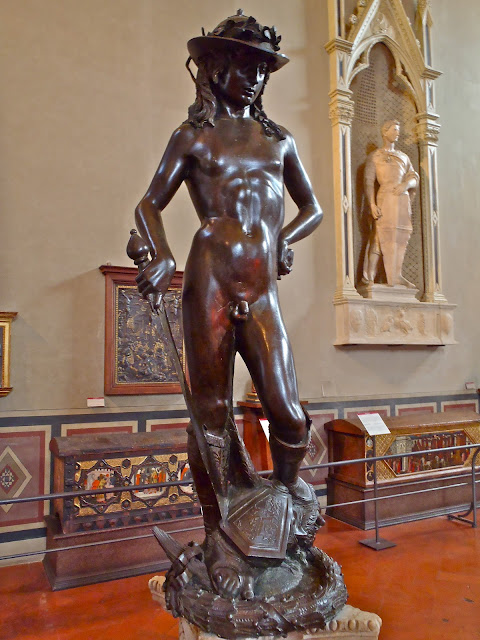 |
David, Donatello, bronze, 1440s, Bargello museum, Florence |
It is often referred to as the first renaissance statue as, in many ways, it shows that the Middle Ages were a thing of the past. But how is bronze cast? It is commonly known how marble is carved, with different shaped chisels and hand drills, but bronze casting is something of a mystery to many. Understanding how it is done renders the works of art even more fascinating.
In the renaissance, as in Antiquity, the artists used the lost wax technique. In the Middle Ages this technique wasn’t entirely lost, but such artefacts were rarely commissioned due to expense and a lack of demand due to the lack of a sophisticated market. There is the direct method and the indirect method of the lost wax technique.
THE DIRECT LOST WAX TECHNIQUE: the sculptor first moulds the desired sculpture shape out of clay. This is called the core. He then covers the whole core with a thin layer of wax and makes all the small details of the sculpture on the wax. Then he attaches wax rods (called sprues) perpendicular to the wax surface covering the core. These will be the chanels from which the air and gasses will escape during the casting process. Iron or bronze pins (chaplets) are also inserted into the wax and the core and remain sticking out. Another layer of clay is then placed over the entire wax covering. The whole structure is then baked and the wax melts. The chaplets are necessary to hold the two clay shells together when the wax melts. A mould has now been created. The whole structure is then banked up with earth or sand to hold it steady and help the mould resist the pressure created when the molten metal is poured in. The mould should also be hot when the metal is poured so that it won’t crack and that the metal won’t cool too quickly and not fill all the mould.
The molten bronze, an alloy of circa 90% copper and 10% tin, is poured into the mould where the wax was, explaining why the technique is called the lost wax technique. The gasses and air escape through the sprues and vents so as not to create air bubbles. The bronze is heated to about 800 degrees celsius (1350-1450 fahrenheit). When the bronze has cooled, the outside clay is chipped off revealing the bronze, which is of course as thick as the wax covering over the core was. Bronze alloy expands before it sets which means that it takes all of the details that were incised onto the wax and picked up by the inner part of the outer clay covering. The clay core is most often scraped out to avoid interior corrosion. The bronze is rough and needs to be finished, which is called chasing. Finally a patina is applied to the chased surface in order to achieve the desired colour. Small statues were directly sculptured in wax, so that when it is invested (covered) with clay and the wax melts, the interior is completely hollow, so the bronze statuette is solid. The limitation of the direct method is that the sculpture is a one off original. There is no possibility for multiple copies to be made as the core and the wax which made the actual detailed statue is ruined during the construction.
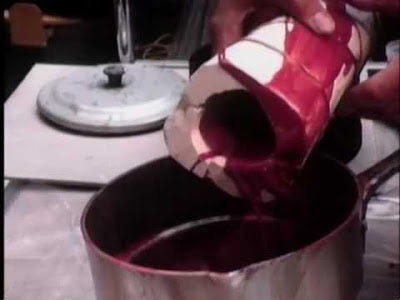 |
Indirect lost wax technique |
THE INDIRECT LOST WAX TECHNIQUE: By the end of the 1400s, the indirect lost wax technique was developed. This enabled copies to be made of the bronze object or statue and it involves a few more steps than the direct method. A second model in wax is required, the so called intermodel, from the original model made by the sculptor. The sculptor takes the original bronze work, or the wax model (in the case of a small object or statuette) and divides the surface mentally into different parts. He then places plaster of Paris (gypsum plaster) or clay over the wax or bronze in the designated segmented areas. It is like a jigsaw puzzle around a 3D. This system is called piece moulding. When the pieces harden and are taken off the surface, the wax or bronze object is saved for further use. The pieces are reassembled and securely bound together and the now empty mould is filled with molten wax to cast the desired intermodel . The wax intermodel will not stick to the piece mould if the plaster is dampened before filling it. After the intermodel is freed from the piece mould, the wax rods which form the sprues are attached. From here, the process proceeds as the direct method. Another option is not to make the core out of solid wax but make the wax a line layer over the piece mould and then to fill the rest of space with clay to make the core. The result will be a hollow bronze object
This was an extremely dangerous process which the artisans performed without all the advanced equipment of today. It also required precision and a huge working knowledge of metals. Armed with the knowledge of the technical process it makes the bronze statues and artefacts all the more precious.